How to create a Purchase Order
Need to create a purchase order? Whether you're starting from scratch, consolidating orders, or using drop shipping, we’ve got you covered! There are several ways to create a purchase order in Orderlink, and we’ll walk you through each of them:
- Create a purchase order from scratch
- Convert a planned order into a purchase order
- Consolidate transfer orders into a single purchase order
- Group customer orders into a purchase order
- Turn a customer order into a drop-shipping purchase order
We’ll break down each method so you can pick the one that works best for you!
Creating individual purchase orders in Orderlink
Click on the "+" button in the top-right corner of the page. Select "Create Purchase Order."
A small window will open, allowing you to click on "Individual" purchase orders.
This will bring up the "Create Purchase Order" page.
Select Supplier and Warehouse:First, select a supplier from the dropdown list. You can also type the supplier's name to quickly find them.
Next, click on the "To Warehouse" dropdown and select the warehouse where the shipment should go.
Set Order Priority and Delivery Date:
Choose an order priority to make it easier to manage later.
If all items will be delivered on the same day, pick a date in the ETA field and check the box next to it.
For items with different delivery dates, you can set different ETAs for each line.
Currency Auto-population:
The currency will automatically populate based on the supplier you selected.
Adding Items to the Purchase Order:
Now, it's time to add the items you want to purchase. Items will appear once you've selected a supplier.
The Supplier Item Number will automatically populate based on your master data settings, and you can manually enter the quantity.
If an item has a price set, it will populate automatically as well.
Create the Purchase Order:
Once you're happy with all the details, click the "Create" button to complete the process.
Bulk Upload Purchase Orders
Click on the "+" button in the top-right corner of the page. Select "Create Purchase Order."
A small window will open, allowing you to click on "Bulk Upload." From here you can download the spreadsheet template to populate with your own Purchase Order data.
Converting a Planned Order to a Purchase Order
To convert a planned order into a purchase order, start by navigating to the "Planner" option in the sidebar and selecting "Planned Orders." Once you're on the Planned Orders page, you can filter the orders by warehouses, suppliers, or order types, making it easier to find exactly what you're looking for.
If you're not quite ready to turn these into purchase orders, you can select the planned orders you want to hold off on and change their status to "Confirmed." This will allow you to work on them later when you're ready.
However, if you're set to move forward, simply select the planned orders you wish to convert. Click on the three dots in the top-right corner and choose the "Create Order" option. This will immediately turn the selected planned orders into purchase orders for further processing.
Consolidating Transfer Orders into One Purchase Order
Check out
this article to combine transfer orders into a single purchase Order in Orderlink
Combining Customer Orders into a Purchase Order
Drop Shipping: Converting Customer Orders into Purchase Orders
How to create an inbound shipment for single or multiple purchase orders?
Orderlink makes it easy for users to combine items from different purchase orders into a single inbound shipment. This process starts with the allocation page, which plays a critical role in ensuring the right quantities are assigned to shipments.
Understanding the Allocation Screen
The allocation panel allows you to control the quantity of stock that will be added to the shipment, based on your supplier's information. You can even give suppliers access to allocate stock directly to your orders.
To get started, navigate to the Orders menu in the sidebar, where you'll find the allocation panel. Before creating any shipment, you need to ensure the stock is properly allocated.
Two Allocation Tabs: Transfer and Purchase Orders
In the allocation panel, you'll notice two tabs: Transfer for transfer orders, and Purchase for purchase orders. You can choose which type of orders you're allocating stock for.
In the Purchase Orders tab, you'll see a column for "Allocated Qty." If the "Allocated Qty" matches the "Required Qty," the order will show as Fully Allocated. However, if you want to adjust the quantity, you can do so by clicking the pencil icon and updating the allocation.
Total Quantity and Value
At the bottom of the table, you'll find the total quantity and value of the allocated stock. This gives you a clear view of what has been allocated so far. Once you're satisfied with the quantities, you can proceed to create shipments.
Filtering Allocated Lines and Creating Shipments
You can filter your orders by "Allocated" status—whether they're fully or partially allocated. This allows you to decide which lines to include in your shipment. If you select lines for different warehouses, the system will automatically create multiple shipments based on the destination warehouses.
Final Step: Create Your Shipment
Once you've selected the allocated lines, simply click on the three dots in the top right corner and select "Create Shipment." That's it! Your shipments are ready, and you can view them in the shipment table, which we'll discuss in the next part of this article.

ASN - Advanced Shipping Notice
First, you'll need to determine whether you need to create an ASN (Advanced Shipping Note) or a standard note. You only need to create an ASN if you're integrated with third-party systems like Mintsoft, Shiphero, or Mainfreight to manage your inventory.
If you're not using any third-party systems and are receiving your purchase orders directly in Orderlink, you can skip the ASN process and check out one of these related articles instead:
Alright, you've made it this far, which means you need to create an ASN (Advanced Shipping Note).
First, navigate to the "International Shipment" option in the sidebar and click on the shipment number for which you need to create the ASN.
Before creating the ASN, make sure that all the items in your shipment are set up in your third-party system, such as Mintsoft, Shiphero, or Mainfreight. Orderlink automatically does one validation when the shipment is created, but if you want to rerun the validation, simply click on the three dots and select Validate ASN. If there are any issues, they will be highlighted in the shipment item lines.
If you encounter any problems, refer to this article to clear the errors in the item codes and rerun the validation.
Once everything is validated and you're happy with it, go ahead and click on the three dots again, and select Create ASN. That's it! You'll see a success notification, and you can now check out your ASN in the ASN tab in the sidebar.

How to update received quantities in a shipment
If you're integrated with third-party systems like Mintsoft, Shiphero, or Mainfreight, your received quantities will automatically update as they are processed in these systems. In such cases, you simply need to approve the receipts to ensure your stock is accurately reflected in Orderlink. For more details on approving receipts from third-party systems, refer to this article.
However, if you are not using third-party systems and want to update received quantities directly in Orderlink, follow the steps outlined below to manually update your received quantities.
To update the received quantities, start by selecting the lines you want to update. Next, click on the three dots in the top right corner and choose "Receive Items." A small pop-up window will appear, allowing you to input the quantities you’ve received.
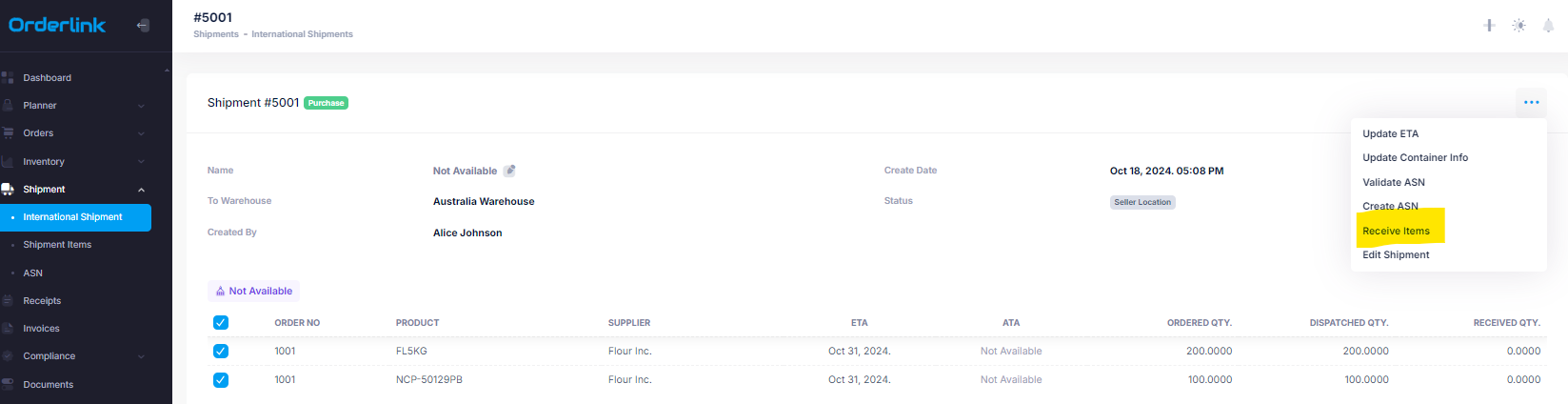
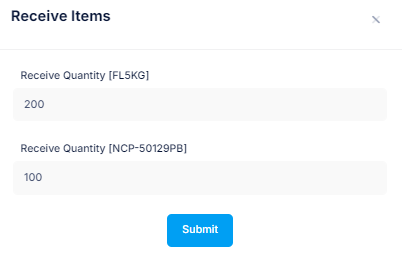
Once you've entered the correct amounts, click "Submit" to record the quantities. Easy, right? But hold on—don’t rush off just yet! While your received quantities are updated, they still need to be approved in order to update your stock levels. This approval step is crucial to syncing with third-party systems like Inventory Planner or ensuring your stock is accurately reflected within Orderlink.
Approve Receipts
This step applies whether you’re using third-party systems or updating quantities directly in Orderlink. To approve receipts, click on the Receipts option in the sidebar. You’ll land on the Receipts Approval page, which is split into two sections: one for Purchase Order Approvals and another for Transfer Order Approvals.
To approve Purchase Orders, simply select the lines you want to approve, click on the three dots in the top-right corner, and choose Approve. This will automatically update the stock levels in Orderlink. If you're connected to third-party systems like Unleashed or Inventory Planner, the quantities will sync and update there as well once approved.